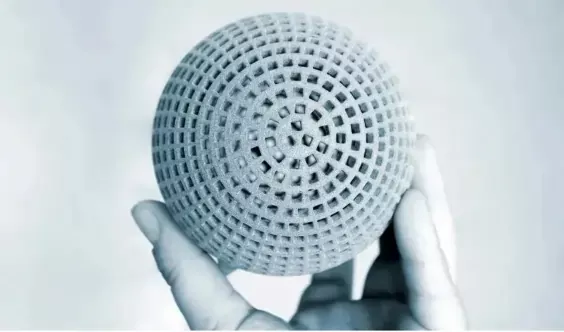
In automotive parts, medical implants, running shoes, or hiking backpacks, we’re seeing an increasing number of 3D printed parts featuring lattice or honeycomb patterns. These lattice structures, often referred to as lattice structures in English, might be considered the latest innovation in 3D printing and additive manufacturing design. In reality, we are constantly surrounded by natural lattice structures: consider honeycombs, snowflakes, fences, sponges, and even the Eiffel Tower. In this blog post, we’ll delve into lattice structures in 3D printing within the context of additive manufacturing design, exploring their types, advantages, and wide range of applications.
Additive Manufacturing Design and Lattice Structures in 3D Printing: A Detailed Guide
Lattice structures (or just lattices) consist of a network of interconnected nodes (referred to as cells) arranged according to continuously repeated or varying patterns, providing advantages in terms of part properties or manufacturing. In traditional manufacturing, lattices are rare because these processes often don’t allow for such complex designs. This is where the power of additive manufacturing lies, making lattices and 3D printing a perfect pair.
Classification and Types of Lattice Structures
Planar Lattices
These lattices are based on a flat, two-dimensional structure that forms a three-dimensional part. Since the layers are printed individually, they might require assembly later. This type of lattice includes tetrahedral patterns, Voronoi lattices, as well as rhombic and hexagonal lattices (e.g., honeycombs).
Space-Filling Lattices (Sare-saring lattices)
These lattices consist of connected segments that form a network by linking the nodes, corners, or edges of cells. Printed layers overlap and interlock. The lattice may need to be reinforced with support materials.
TPMS (Triply Periodic Minimal Surface) Lattices
These lattices are based on a trigonometric equation that defines the cell. The basic shape of the lattice can vary and can create highly complex, organic-looking structures.
Characteristics and Application Criteria of Lattice Structures
Lattices can also be classified as periodic or stochastic. Periodic lattices maintain a uniform pattern throughout the structure, while stochastic lattices have variations in cell shape, size, and arrangement to reinforce the structure in specific directions.
The choice of lattice depends on its ultimate purpose. The design considers the desired stiffness, as well as appropriate geometry and size. The compression behavior, meaning how the structure performs under pressure and in which directions, is also analyzed. Additionally, whether the lattice can absorb energy in case of deformation is often a key question. These criteria are of great importance in the additive manufacturing design process.
Design and 3D Printing of Lattices
A specialized design tool is necessary for designing lattices for 3D printing. While some modeling software offers basic functionalities for lattices, software specific to topology optimization or generative design is more reliable. Generative design calculates the optimal design for the part based on the required properties and the chosen printing method. If the design includes a lattice, its cells, densities, and arrangement are also calculated.
Many tools are available for optimizing 3D models and creating lattice structures, including Autodesk Within, nTopology’s nTop, Meshify, Core Technology’s 4D_Additive, Netfabb, or Hyperganic’s HyDesign. The design choice will depend on the application, material, and printing technology.
Production Challenges and Solutions for 3D Printed Lattices
3D printing makes the production of lattice structures much easier, as they are typically very complex and intricate. Additionally, printing lattices is faster than solid structures. Theoretically, a wide variety of printing materials and technologies can be used, but each process imposes its own characteristics:
- In FDM and SLA printing, support structures may be required for large lattice structures.
- In powder-based processes like SLS or MJF, sufficient access points must be provided to allow for effective depowdering.
- In DMLS, additional supports should be considered to avoid 2 mm limits for unsupported bridges.
These characteristics are generally taken into account from the additive manufacturing design stage.
3D Printed Lattice Applications and Use Cases
Now, let’s move on to a few application areas where 3D printed lattices demonstrate their potential. In the medical field, lattices are used not only for implants, as mentioned earlier, but also for prosthetics and orthotics to optimize weight, strength, or comfort.
Lattice structures are particularly advantageous in applications requiring high performance and lightweighting, such as the automotive, aerospace, and space industries. For instance, thanks to nTop’s “Shell & Lattice” feature, Aerojet Rocketdyne successfully reduced the weight of a quadruple engine block by 67% and cut production costs by 66%.
However, lattices are also gaining importance and popularity in the fields of sports and consumer goods. We are seeing more and more protective equipment and 3D printed lattice infills. These lattices are found in bicycle saddles, helmet padding, protective clothing, etc., and also in the midsoles of shoes. We particularly hope for better energy transfer and increased performance for running shoes.
This logic also applies to car seats or backpacks. For example, outdoor equipment specialist Oechsler used Materialise’s Magics tool to increase the comfort of innovative backpacks thanks to lattice structures. Furniture is also starting to integrate lattices, though in this case, aesthetics seem to take precedence over lightweighting.
These examples demonstrate that lattices are already present in many applications. As the industrialization of 3D printing progresses and design possibilities continuously evolve, this trend should not only continue but also intensify in the future. Especially by using sustainable materials like recycled wood to produce wood powder filaments, new horizons can be opened in this field.