Plastic Injection Molding | Precise and Efficient Production | MARM Engineering
Plastic injection molding is an indispensable mass production method for the mass production of plastic parts. In this process, preferred by many sectors such as automotive, white goods, furniture, machine manufacturing and medical, we provide the production of high-precision and quality plastic parts by using our expertise and advanced equipment.
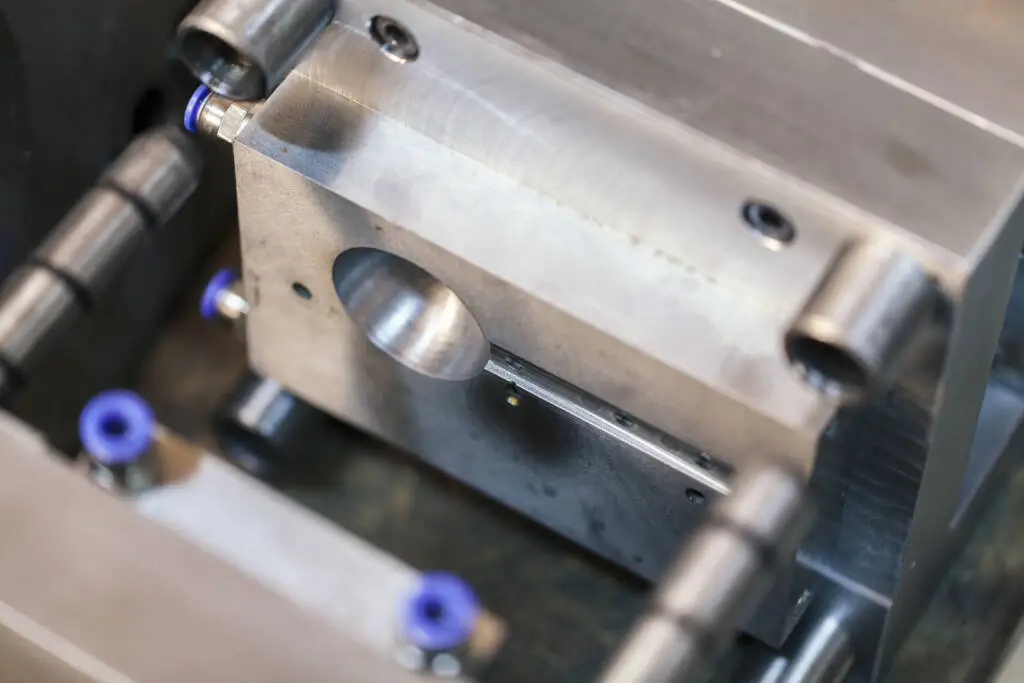
Plastic Injection Mold Machine: Precision and Efficiency in Mass Production
Plastic injection mold machine is a high-precision production tool that forms the heart of mass production of plastic parts. These machines, used in countless sectors from automotive to medical, from white goods to packaging, are indispensable to meet complex designs and high-volume production needs. With our latest technology plastic injection mold machines, we bring your projects to life with the highest level of quality and efficiency.
How Does a Plastic Injection Mold Machine Work?
A plastic injection machine fundamentally consists of three main sections: injection unit, mold clamping unit, and control unit. The process typically includes the following steps:
- Plastic Injection Raw Material Feeding
Plastic granules (thermoplastic material) are loaded into the machine’s hopper.
- Plastic Injection Heating and Melting
Granules are heated and melted inside a heating cylinder. A screw mechanism pushes the molten plastic forward.
- Injection into the Mold
Molten plastic is injected under high pressure into a steel or aluminum mold that was previously prepared and mounted on the machine. The mold typically consists of two halves (fixed and movable plate)
- Plastic Injection Cooling and Solidification
The injected plastic rapidly cools and solidifies, taking the shape of the mold, thanks to the cooling channels inside the mold.
- Part Ejection from the Mold
When the part has cooled enough, the movable plate of the mold opens, and the molded part is automatically ejected from the mold using ejector pins.
- Cycle Repetition
The mold closes and becomes ready for the next cycle. This cycle repeats in seconds, ensuring mass production.
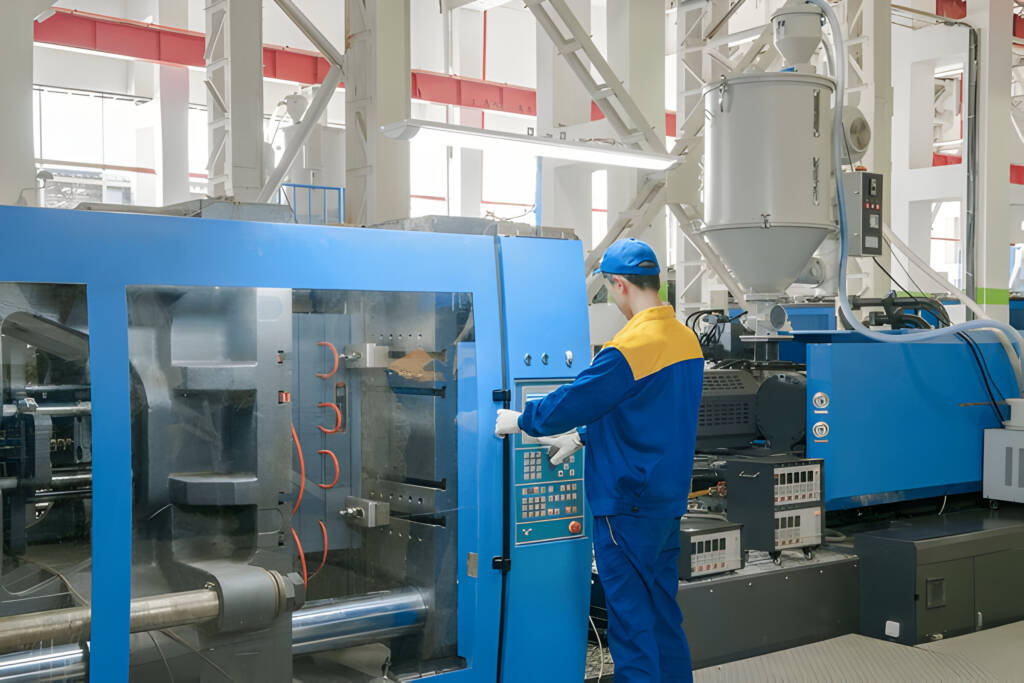
Plastic Injection Molding Steps
Our plastic injection molding process progresses with transparent and meticulous steps from idea to final product. This flow combines the rapid feedback loop in the prototyping stage with the efficiency of the CNC mold and injection machine process, offering you maximum quality and flexibility.
3D Design & Rapid Prototyping
The desired part’s function and dimensions are prepared as a 3D CAD model by our design team. This digital model is rapidly materialized into a physical prototype using 3D printing (FDM/SLA) technology to obtain the final prototype before production. Thus, before moving to mold production, form, fit and function tests are completed, preventing costly revisions. This stage is a critical step that provides time and cost savings. We see the importance of 3D printing here.
High Precision CNC Mold Production
Taking the approved prototype as reference, molds are machined with high precision on CNC machines from aluminum or steel blocks. Mold channels, surface smoothness and tolerances are subjected to strict quality controls for consistency and long life in mass production. This stage forms the basis of the final product quality and production efficiency to be achieved.
Injection Machine Integration & Mass Production
The prepared mold is meticulously integrated into the plastic injection molding machine; cooling circuits and sensors are connected correctly. Thermoplastic raw material is injected into the mold under controlled pressure and temperature. With automatic cooling, mold opening-closing and part holder processes, high quality, repeatable plastic parts are produced in seconds. Thus, high volume and consistent production are guaranteed.
Frequently Asked Questions (FAQ)
Why is 3D printing needed before mold production?
3D printing enables rapid testing of a design’s form, fit, and function. This allows design flaws, assembly incompatibilities, and ergonomic deficiencies to be identified and corrected before proceeding to mold production.
How does the CNC mold machining process work?
Material Selection: Stainless steel or aluminum block CAM Programming: Tool paths are prepared based on CAD data Roughing (Material Removal): Large excess material is removed with fast rough machining Finishing (Surface Treatment): Fine cuts ensure surface smoothness and adherence to tolerances Quality Control: Channels, surface tolerances and rigidity are verified with measurement devices
How many products can I get per day in mass production?
Daily production quantity depends on the cycle time. For example: In 30 seconds cycle time: theoretically 2,880 units/24 hours In practical conditions (operator breaks, maintenance etc.): approximately 2,000–2,500 units/day
Can mass production be done with 3D printing?
Yes. 3D printing is ideal for prototyping and low-volume custom parts. It can be used for low-volume mass production, offering high speed and consistent quality.