What Is MJF Technology? – 3D Printing with Multi Jet Fusion
Multi Jet Fusion (MJF) is a 3D printing technology that combines thermal inkjet deposition and powder-bed fusion methods. MJF enables the rapid, precise production of complex-geometry, high-quality plastic parts. It delivers high resolution, fast throughput, and robust end-use components—ideal for applications ranging from prototypes to final industrial products.
Stages of MJF Technology
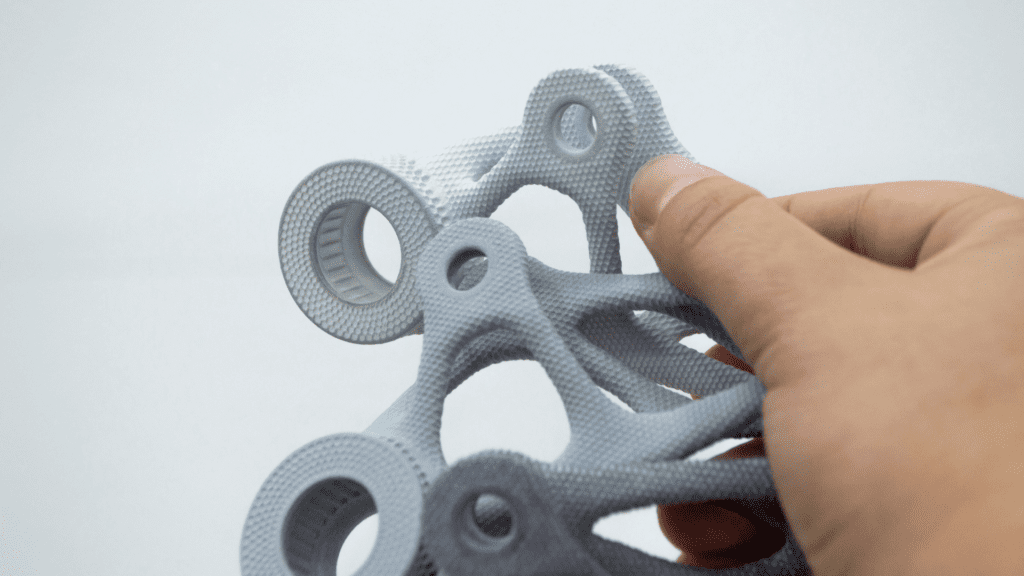
Powder Preparation
The process begins by preparing the polymer. The chosen material is conditioned to ensure the correct particle size distribution and flow characteristics for consistent layer deposition.
Print Bed Creation
A build platform is established and a thin layer of powder is spread evenly across the bed, ready for the first pass of the printhead.
Thermal Inkjet Application
A thermal inkjet printhead selectively deposits fusion and detailing agents onto the powder bed. The fusion agent causes targeted areas to melt and fuse, while the detailing agent refines edges and surface finish.
Light Windows and Heated Rollers
Underlying light-transmissive windows and heated rollers maintain the powder bed at precise temperatures. Light windows allow infrared energy to penetrate and control local heating, while rollers ensure uniform bed temperature and density.
Layer Fusion
After agent deposition, another powder layer is spread and the fusion cycle repeats. Layer upon layer, the part builds up with micron-level accuracy and consistent mechanical properties.
Cooling and Cleaning
Once printing is complete, the entire build cools in the powder bed. Parts are then removed, excess powder is brushed or blown away, and components proceed to any required post-processing or finishing steps.