Istanbul Kadikoy FDM Filaments: PLA, ABS, TPU & PETG
In this comprehensive list that guides you in choosing FDM filament, we have included the printing temperatures, mechanical properties and prominent advantages of all materials from PLA to PAHT CF15. Whether it is a prototype or final product production, you can easily determine the most suitable filament type for the requirements of your projects.
Choosing the right filament optimizes the melting and cooling behavior of the material in the layered production process, providing high print quality and smooth surface roughness; in addition, it enables the mechanical properties such as strength, flexibility or heat resistance to be fully met according to the intended use. When an unsuitable filament is preferred, it causes problems such as blockage, layer separation or warping in printing, causing both time and material loss.
If you are looking for both economical and performance-oriented material alternatives for your 3D printing projects in Istanbul; We invite you to discover the most suitable FDM filaments for your needs with Kadıköy delivery, urgent order and technical support options. Request a free sample for more!
FDM Material List
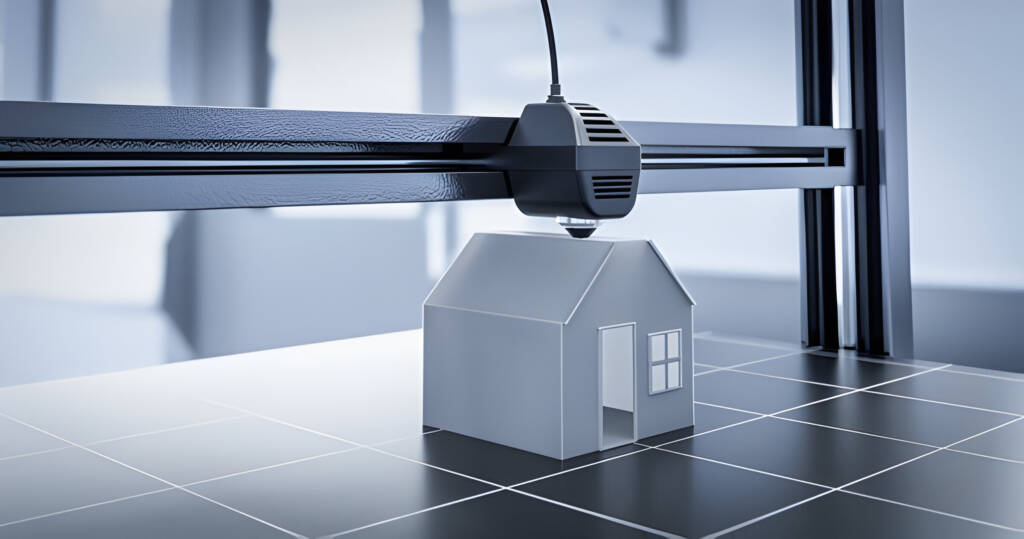
The FDM Material List was prepared to help you choose the most suitable filament type for the performance, durability and aesthetics you need in your 3D printing projects. This list, which covers a wide range from PLA to PLA Pro, ABS to TPU; PETG, ASA, PET, PA (Nylon), carbon fiber reinforced PAHT CF15 and PC–ABS FR to advanced materials, provides summary information about the printing temperature, mechanical properties, flexibility/hardness balance and application areas where each filament is suitable for use.
Thus, you can save time and money by making the right material selection both in the prototype development phase and in the production of functional final products. You can contact us for more detailed specifications and ordering information.
Available Filament Materials and Properties
Printing Temperature: 180 – 220 °C
Advantages: Biodegradable, low warping, aesthetic surface
Disadvantages: Moderate mechanical strength, low heat resistance
Printing Temperature: 200 – 230 °C
Advantages: Increased mechanical strength and heat resistance, less brittle
Disadvantages: May require fine-tuning, costs more than standard PLA
Printing Temperature: 220 – 250 °C
Advantages: High impact resistance, good heat resistance
Disadvantages: Warping, print odor; indoor and heated bed recommended
Print Temperature: 210 – 230 °C
Advantages: Flexible and elastic, ideal for shock absorbing applications
Disadvantages: Low print speed, requires precise retraction settings
Print Temperature: 230 – 250 °C
Advantages: High chemical resistance, low warping, stiffness-flexibility balance
Disadvantages: High temperature, can be stringing
Print Temperature: 260 – 280 °C
Advantages: 15% carbon fiber reinforced strength and heat resistance
Disadvantages: Abrasive; hardened nozzle and controlled environment recommended
Print Temperature: 240 – 260 °C
Advantages: UV and weather resistant, ideal for outdoor use
Disadvantages: Warping; closed press room and heated bed required
Print Temperature: 230 – 250 °C
Advantages: Transparent, lightweight, chemically resistant and suitable for food contact
Disadvantages: Moisture absorbent; pre-print drying required
Print Temperature: 240 – 260 °C
Advantages: High durability, flexibility and abrasion resistance
Disadvantages: Quickly absorbs moisture; requires drying and good adhesion surface
Printing Temperature: 250 – 270 °C
Advantages: Flame retardant, high impact and heat resistance
Disadvantages: High temperature, good ventilation and closed environment recommended
Frequently Asked Questions (FAQ)
Which filament material should I choose for 3D Printing?
PLA or PLA Pro is generally sufficient for prototypes, while ABS or PAHT CF15 is preferred if high heat resistance and mechanical strength are required. TPU is ideal for flexible parts, while PETG and ASA are ideal for applications with chemical contact. You can make your material selection according to your project requirements with a simple checklist.
How long does it take to deliver if I order filament from Istanbul?
Orders placed from our Kadıköy central warehouse are delivered to your address on the same day or within 1 business day at the latest. Delivery within 4–6 hours is also possible with the express shipping option.
Can I buy filament in bulk in Kadıköy?
Yes, we also offer bulk purchasing, custom color mixing and packaging services from our Kadıköy office. You can contact us for detailed offers and delivery options.
What are your custom color and fill ratio options?
In addition to standard colors, we produce custom colors in pastel, metallic and fluo tones. You can personalize the aesthetics and mechanics of your part with our carbon fiber, glass fiber or wood-filled core filaments.