DFAM: 3D Design and Printing Services with Precise Layer Adjustment
Within the framework of 3D Design and Printing Services, you can produce and manufacture lighter, stronger and more economical parts using 3D printing and design services and Additive Manufacturing Custom Design (DFAM) principles.
DFAM Based 3D Design and Printing Services with Precise Layer Adjustment
With our 3D Design and Printing Services and deep expertise in 3D printing and design services, we optimize your parts in terms of performance, cost and production speed using layer-by-layer design parts. Click WhatsApp for more information!
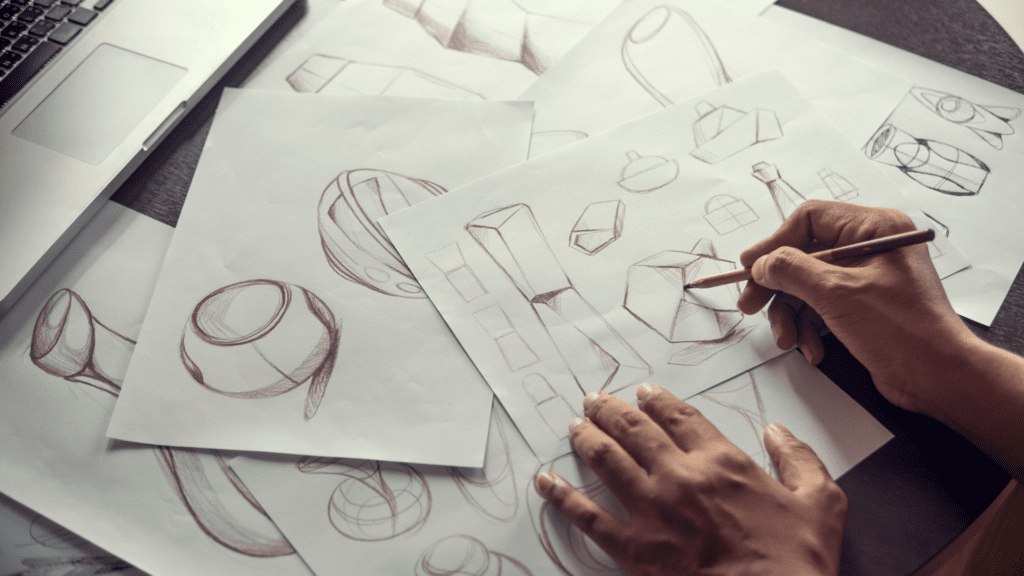
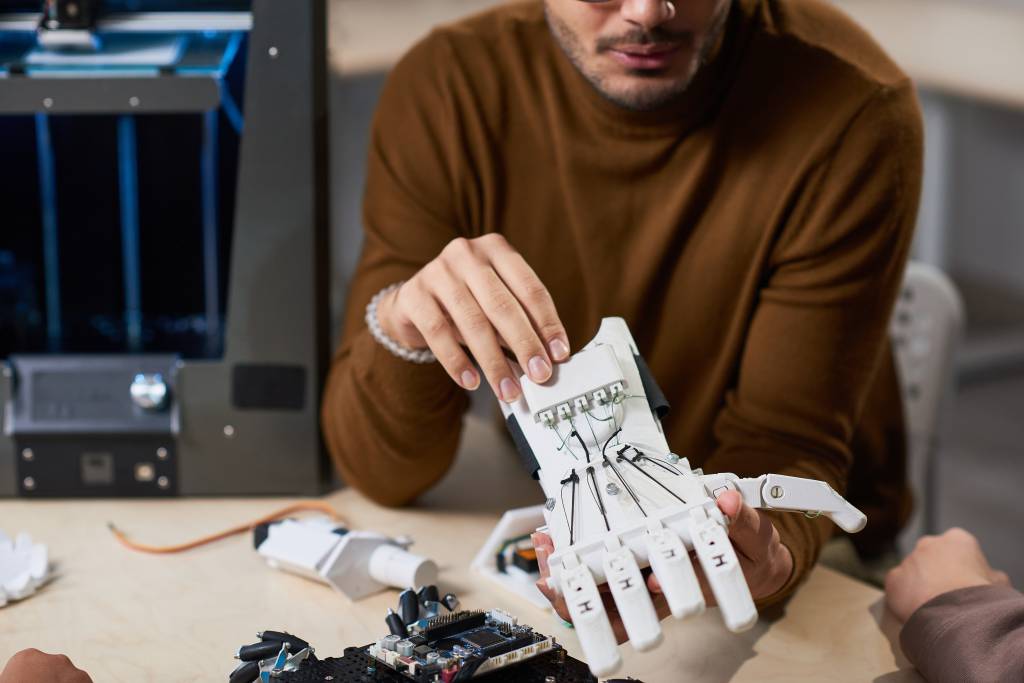
What is DFAM?
Design for Additive Manufacturing (DFAM) is an approach that adapts the design from head to toe to the additive manufacturing logic of 3D printing technology. Geometries that push the design boundaries in traditional machining and casting methods are easily realized with DFAM.
Within the scope of our 3D design and printing services, each part is optimized according to DFAM principles and provides the best result in terms of both performance and cost.
DFAM's Main Goals
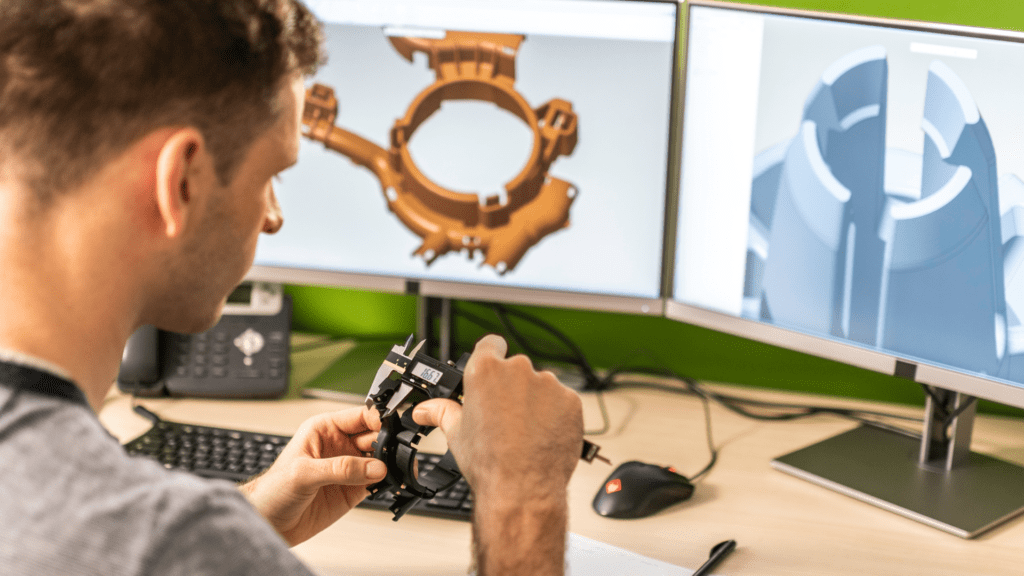
Maximizing the Advantages of 3D Printing Technology
- Material Efficiency: Lattice and skeleton structures reduce infill ratios; weight is reduced while strength is maintained.
- Complex Geometry Production: Single-piece assemblies, internal channels, organic forms, details that are considered impossible in traditional production, are designed without any problems Get a Quote!
Optimizing the Design Process
- Printing Time & Cost Management: Layer thickness, support requirement and printing direction are determined during the design phase; thus, time and material are saved during the 3D printing and design services process.
- Functional Integration: Assembly steps and error risks are minimized by integrating multiple parts into a single component.
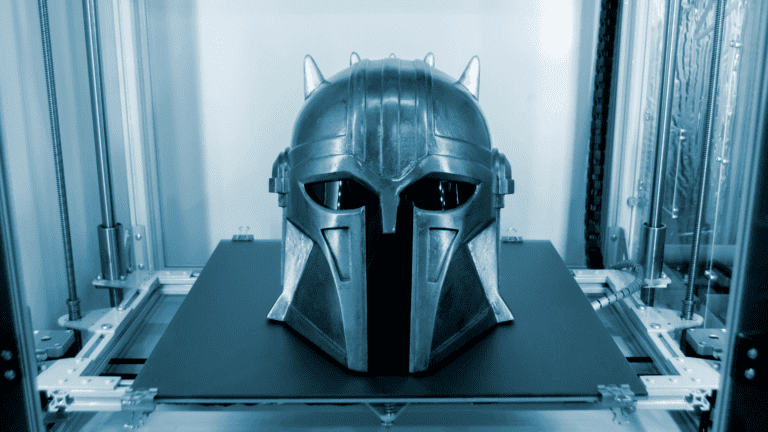
DFAM Process Steps
1. Preliminary Design and Material Selection
Filling of thermoplastic, metal powder or composite materials according to application conditions. Whether you have your own 3D model file or ready 3D printer printing models from popular 3D model sites, we are here for all your projects. Click WhatsApp for more information!
2. Topology Optimization and Lightweight Structures
Software tools (nTopology, Altair Inspire) analyze load-bearing areas. Unnecessary volumes are removed; internal skeleton structures are defined, resulting in a 50–70% weight reduction.
3. Print Orientation and Support Design
Critical areas of the part are positioned according to the printing direction; interlayer adhesion and surface quality are optimized. These optimizations ensure flawless printing quality for models provided through 3D design sites or created by you. Support structures are also designed to be easily separable, which significantly reduces post-processing time. Click Now!
4. Finishing and Quality Control
Processes such as sinter, temper, coating and sanding are planned. Part quality is confirmed by measuring tolerances with CMM or optical scanning.
Sample Case Studies
Aviation Application
GE Aviation redesigned and manufactured a titanium propeller hub in one piece with DFAM; reduced weight by 25% and eliminated assembly steps.
Medical Implant
Both bone integration was facilitated and 40% weight saving was achieved by designing the skull implant with an internal lattice structure.
Conclusion and Further Reading
- nTopology DFAM Resources
- Autodesk Netfabb Training Documents
- Additive Manufacturing Technologies (Gibson, Rosen & Stucker)
- SIEMENS Generative Design Studies
Frequently Asked Questions About 3D Design
Design for 3D printing (DFAM) optimizes parts for the additive process—accounting for internal voids, lattice structures, and support needs up front. Traditional design focuses on subtractive processes like machining or casting, with their own tooling and draft-angle constraints.
Key factors include layer thickness adjustment, print orientation, and support design; material selection; minimum wall thickness; and tolerance definitions. Optimizing orientation and support break-away characteristics also reduces post-processing effort.
Well-crafted DFAM designs cut print time and material usage, boost mechanical performance and surface finish, and minimize support structures—drastically reducing post-processing time, overall cost, and delivery lead times.
Topology optimization analyzes where the part needs to bear loads and removes all unnecessary material. Software like nTopology or Altair Inspire uses defined loads and constraints to automatically generate the optimal geometry.
Lattice structures dramatically lower part weight while preserving strength. They are ideal in low-load regions, for aesthetic or thermal-management needs, and in applications requiring energy absorption or flexibility.
Print direction influences interlayer adhesion strength, surface roughness, and support volume. Determining orientation based on critical surfaces (holes, thin walls, overhangs) ensures optimal adhesion and minimal supports.
Orient the part at self-supporting angles, reduce overhangs and protrusions, and choose break-away or soluble support materials to simplify post-processing.