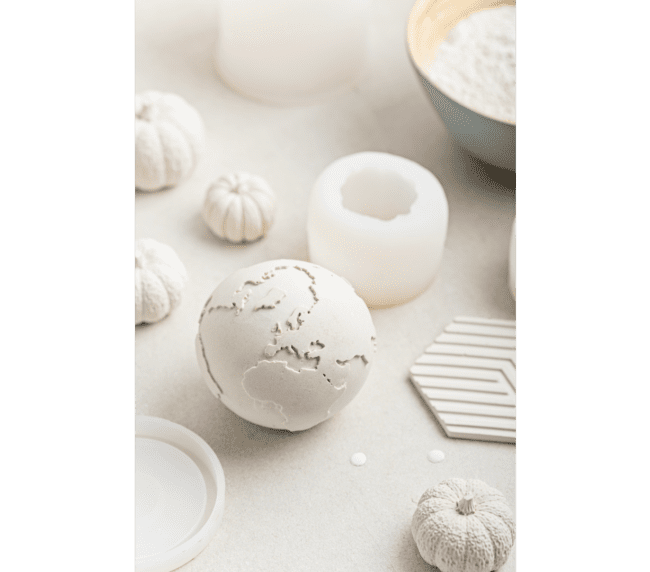
Precision Detail and Superior Flexibility in Silicone Molding
Silicone molding, which has a unique position among molding methods, stands out with its superior flexibility and ability to capture fine detail, especially for silicone molding services. Thanks to these features, it becomes possible to perfectly reproduce complex and delicate forms in areas such as prototyping, sculpting, toy making and home decoration industries. Silicone molding overcomes the limitations of traditional methods and creates durable and flexible molds that preserve even the smallest details.
Step-by-Step Silicone Molding Process
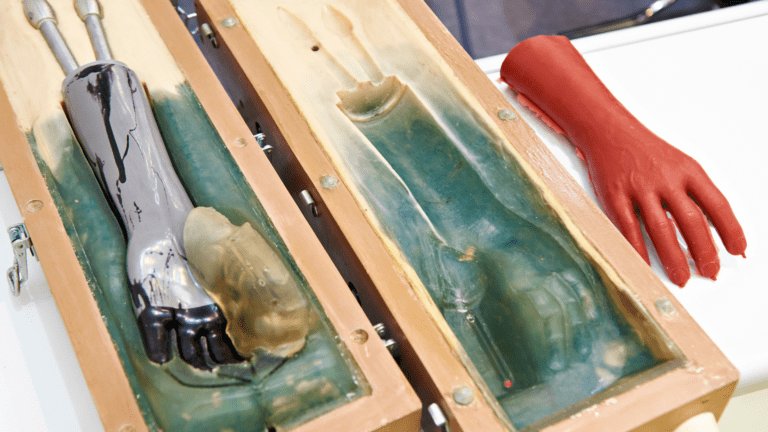
- Object Production
- The approved 3D Model is printed via FDM or SLA technology for prototyping.
- The printed master is sanded to remove layer lines and, if needed, primed.
- This master then serves as the reference that determines the final mold quality for sculptures, toys, or décor pieces.
- Mold Jacket Creation
- Mold Preparation & Silicone Casting
- The selected silicone formulation (e.g., Shore A20–40) and catalyst are mixed and degassed under vacuum to remove bubbles.
- The degassed silicone is poured slowly into the mold jacket, taking care to avoid air pockets and ensure full detail reproduction.
- The assembly cures at room temperature (or at 60 °C) for 2–4 hours, yielding an elastic mold that flawlessly captures every detail.
- Casting & Final Part Removal
- Once cured, the silicone mold is removed from the jacket and the master is extracted, leaving the cavity ready for casting.
- The chosen material (resin, plaster, soap, wax, etc.) is poured or injected into the mold; vacuum may again be used to eliminate bubbles.
- After the material sets, the mold is carefully opened, the finished piece is demolded, and any flash is trimmed for a perfect final product.
What Can Be Cast in Silicone Molds?
- Resin & Polyurethane: Preferred for high-detail parts with mechanical strength.
- Plaster & Polyester: Cost-effective, easy to work with for sculptures and decorative objects.
- Food-Grade Silicone: Safe for casting chocolate, candies, or candles.
- High-Temperature Silicones: Used for hot wax casting, metal prototypes, or industrial applications.
- Abrasion-Resistant Hybrids: Ideal for molds requiring extended durability. Request a quote!
Advantages of Silicone Molds in a Digital Workflow
- Digital Archiving: Your 3D Model files are stored in the cloud—five years later you can reproduce the same mold instantly.
- Parametric Revisions: Dimensions, wall thicknesses, and fine details can be updated in software and used to generate a new mold jacket.
- Remote Service: Design approvals and file transfers happen online, enabling rapid delivery once materials arrive.
- Cost & Time Savings: Perfecting the digital model up front minimizes rework and reduces mold printing costs.